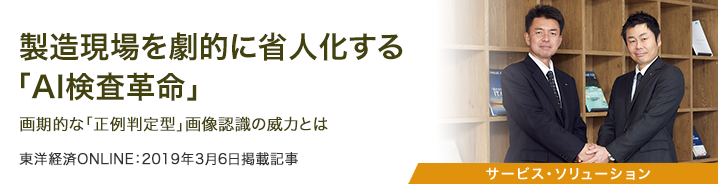
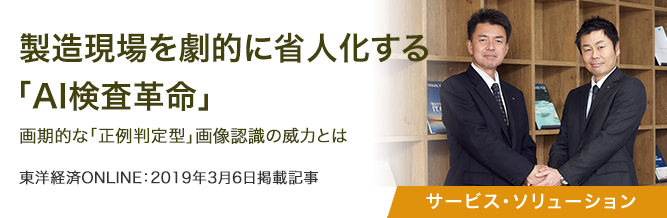
検査・検品の共通課題「人手不足」の解消に向けて
ものづくりの現場で欠かせない作業の1つが、検査・検品だ。不良品が出荷されないようチェックする重要な工程であり、その精度の高さが製品の品質・信頼性につながっている。とりわけ昨今は、グローバルレベルで市場競争が激化。瑕疵(かし)のある製品を出荷することによるリスクは甚大なものがあるため、製造業界各社はどこも検査・検品に力を注いでいる。
とはいえ、検品の精度を維持するのは並大抵のことではない。画像処理を利用した検査装置による検査自動化の取組みは早くから進められてきたが、適用領域が限定され、最終的には「人の目」に頼らざるを得ないケースも多い。しかし、単純に人がいれば成り立つレベルではなく、いわば品質保持の最終ラインとも呼べるポジションであるため、高いスキルが求められる。
しかし、人手不足が慢性化している現在、十分な人員を確保するのは難しい。検査・検品担当者の辞職や病休などで出荷量が大幅に落ちてしまうケースもあるなど、「人の目」への依存は意外とリスクが高い。全国の製造現場をつぶさに見ているメカニカルパーツの総合商社、日伝の濱田善夫氏は次のように指摘する。
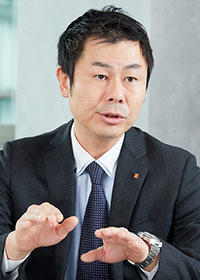
日伝
濱田善夫氏
「少子高齢化や人口減少社会への突入で、毎年数十万人単位で労働力人口が減っています。今や、人手不足は大手・中小の規模を問わず共通している深刻な悩みなのです。従来、製造現場ではコストダウンのために省人化を目指していましたが、現在はどの現場も、少ない人手でいかに安定した生産体制を整えるかに必死となっています」
例えば、親会社からの生産量増量の要請に対し、検品要員が不足しているため対応できない中小事業者も少なくないという。そうした現場の悲痛な声に応えるべく、新たなソリューションを模索してきた日伝が見いだした活路がAIだと濱田氏は明かす。
「現在、製造現場で検査の自動化を担っている画像処理機は、プログラミング形式です。NG例に対するチェック方法を設定し、不良品を検出するわけですが、設定されたものにしか反応しない欠点がありました。その点AIならば、どんどん学習させることで、今まで検出できなかったレベルの不良品にも対応できます。そうすることで、今まで属人化していたスキルを定量化でき、『人とAIの共生』を目指せると考えています」
運用コストを劇的に低下させる「正例判定型」
単に省人化を実現するだけでなく、検査・検品の品質を安定化させたい――。2つの課題を解決するツールを探していた日伝が、いろいろなAIプラットフォームを試した末にたどり着いたのが、NTTコムウェアのAI画像認識プラットフォーム「Deeptector®(ディープテクター)」。同種のサービスはほかにも多いが、どのように違うのだろうか。NTTコムウェアの佐々木秀紀は、こう説明する。
「4種類の判定パターンを用意しているのが、強みのひとつです。企業が抱えるビジネス課題は千差万別ですので、画像認識を適用するにしても課題に沿った提案でなければ意味がありません。解決したい課題によっては、複数の判定パターンを組み合わせてご提案するケースもあります」
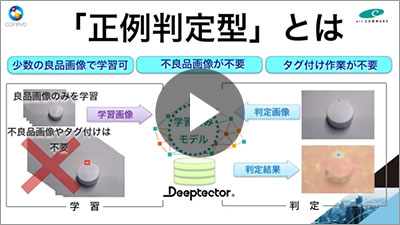
画像認識AI「Deeptector®」正例判定型のご紹介。その他の判定パターンなど詳細はこちらから
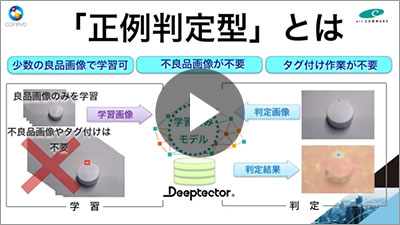
画像認識AI「Deeptector®」正例判定型のご紹介。その他の判定パターンなど詳細はこちらから
4種類の判定パターンとは、「検出型」「分類型」「レベル判定型」「正例判定型」。なかでも「正例判定型」は画期的だ。従来、スタンダードだった「検出型」が、多数の不良品画像を学習させ、トライアンドエラーで判定精度を上げていくチューニング過程を避けて通れなかったのに対し、正常品だけを少数学習させる。つまり、事前に想定できない不良も含め、正常品以外の製品をすべて検知できるのである。まさに逆転の発想といえるこの判定パターンは、AI導入コストおよび導入後の運用コストを圧倒的に低く抑えることが可能だと佐々木は話す。
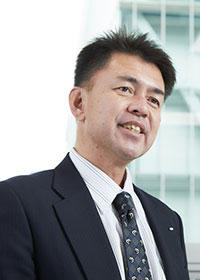
NTTコムウェア
佐々木秀紀
「画像認識AIで一般的な『検出型』ですと、不良の種類ごとに数百枚から数千枚の画像を学習させる必要があります。そのため、莫大な画像データが必要です。さらに、どの部分が検出対象(キズ、汚れなど)なのかを学習用画像に対して指定する『タグ付け』と呼ばれる作業を1枚ずつしていかなければなりませんので、どうしてもコストがかさみますし、効果を発揮するまで一定の時間がかかります。しかし、『正例判定型』ならば必要な画像は数枚から数十枚あれば十分ですし、日々製造内容が変わるラインでも、その日の始まりに正常品を学習させれば運用できる可能性があります」
濱田氏も、この「正例判定型」には驚きを隠さない。とくに、新製品の検査・検品にかかっていた負担を劇的に軽減させる可能性があるという。
「新製品は、製造しながら不良品の基準を見つけていかなければなりませんので、どの企業もダブルチェック、トリプルチェックの体制で取り組んでいます。そして、神経をすり減らしながら不良、不具合を確認していくわけです。でも『正例判定型』なら、そうした体制をわざわざ組む必要がなく、『怪しい仕上がりはすべて取り除く』ことができます」
そもそも、日本のものづくり現場では不良品がほとんど出ないケースもある。不良品の発生頻度が数年に1回という工場もあれば、不良品が出た時点で製造ラインそのものを改善するため同じ不良は出さないという工場もある。そうした製造現場での検査を自動化させる場合、「Deeptector®」の「正例判定型」が重宝されることは容易に想像できよう。
※「Deeptector®」の利用イメージはこちらから
協業でAIの効果を最大限に発揮するソリューション開発も可能に
さらに、メカニカルパーツに強い日伝のような企業とパートナーシップを結ぶことで、「AIができること」にとどまらないソリューションを創出できるのも見逃せない。佐々木は次のように話す。
「AIだけで課題が解決できるわけではありません。画像認識AIが効果を発揮するには、入力画像の質を上げることが重要ですし、仮にAIで不良品を感知しても、そのままラインを流れてしまえば無意味です。カメラや照明などの撮像環境から、不良品検知後の表示や通知、さらには不良品の排除、例えばロボットアームによる除去やコンベア切り替えによる排出までを提案していくことが必要です。製造現場への設備提案などで豊富な経験をもつ日伝さんと積極的に連携しようとしています」
濱田氏は、これまで解決できなかった顧客企業の課題を解決できる手応えを「Deeptector®」に感じているようだ。
「コストや手間がかかりすぎるという理由で、検査・検品の省人化をあきらめていた企業はたくさんあります。でも、『Deeptector®』ならより精度の高いソリューションを、周辺機器を含めてトータルにご提案できます。AIでの再チャレンジをどんどんサポートし、新たなビジネスを展開していきたいと思っています」
AI導入のハードルとなっていた大量画像収集やチューニングが不要で、現場で使われているシステムと柔軟に接続できるAPIを備えているなど、導入・運用までのプロセスが簡易化されているのも製造現場にとっては大きなメリットだ。そのため、AI技術者がいなくても運用ができ、同種サービスと比べて圧倒的に導入のハードルは低くなったといえる。インストール版とクラウド版が用意されており、ニーズや製品の性質に合わせて選べるのもありがたい。
※「Deeptector®」の利用までの流れ
また、製造現場の過酷な環境における連続運転にも耐えられるサーバーを展開する日本HP社と連携し、「Deeptector®」をインストールさせたモデルも販売。電源とネットワークに接続するだけで、すぐに学習開始が可能と手軽なうえ、気温50度となる工場でも24時間運転させられるのが魅力だ。
「これまで目視で点検していたのをAIに置き換えるというのが、『Deeptector®』のご提案です。AIによるデジタルトランスフォーメーションを実現させ、安定生産体制の維持および製品品質向上を促す業務改革のお手伝いをさせていただきたいです」(佐々木)
【 制作/東洋経済企画広告制作チーム 】
2019/4/23
- ※ 商品およびサービスの内容は、予告なく変更する場合がありますので、あらかじめご了承ください。
- ※ 「Deeptector」「SmartCloud(スマートクラウド)」「SmartCloud」ロゴは、NTTコムウェア株式会社の登録商標です。
- ※ その他、記載されている社名、商品名などは、各社の商標または登録商標である場合があります。